OSSIDAZIONE ANODICA DURA: IL PROCESSO E LE CARATTERISTICHE
L’ ossidazione anodica dura è una versione modificata della classica ossidazione solforica.
Si effettua operando a temperatura di zero gradi utilizzando elevate densità di corrente.
La nostra ossidazione dura supera le prescrizioni per l’ossidazione secondo UNI EN ISO 7599 e ASTM Type III.
Tutti i nostri processi di ossidazione ELANOX® sono eseguiti con un processo modificato che conferisce elevata tenuta a corrosione sia in campo alcalino che acido. I nostri processi superano l’Alkaline dip test a pH 13,5 prescritto dalle principali case automobilistiche, mentre in campo acido resistono bene ai succhi acidi presenti nel settore alimentare, come aceto, succo di limone ecc..
Nella versione ELANOX® H e ELANOX® HW il trattamento può essere fornito a richiesta, con strato superficiale di ossido con caratteristiche antibatteriche.
Le altre caratteristiche tipiche sono:
- Elevato spessore possibile.
- Alta durezza superficiale.
- Elevata resistenza all’usura ed all’abrasione.
- Tenuta alla corrosione da molto alta ad elevatissima in funzione della lega, dello spessore e delle varianti utilizzate.
- Elevata capacità di isolamento elettrico.
- Eccellente capacità di dissipazione termica nel campo dell’ infrarosso.
- Compatibilità con alimenti
Utilizziamo i processi Elanox®, nelle loro varianti, scelte in funzione delle caratteristiche richieste sul particolare trattato.
ELANOX® H processo standard ottimizzato.
Processo di ossidazione dura ottenuto con tecnologia proprietaria di controllo in corrente, per impieghi standard.
ELANOX® HW processo adatto per alti spessori.
Versione a potenza superficiale controllata. Consente di ottenere spessori elevati limitando la sollecitazione termica dello strato di ossido in corso di formazione, massimizzando le caratteristiche di resistenza dello strato di ossido.
ELANOX® HP strato modificato – maggiore tenuta a corrosione.
Processo effettuato con tecnologia proprietaria di controllo in corrente, ma che consente di ottenere uno strato modificato in grado di migliorare la resistenza alla corrosione.
ELANOX® HD processo esclusivo con altissima tenuta a corrosione.
Versione del processo che conferisce maggiore resistenza superficiale, riduzione del coefficiente di attrito e altissima tenuta a corrosione.
LE LEGHE TRATTABILI
Possono essere trattate tutte le leghe, con eccezione della serie 2000. Queste leghe devono essere trattate con bagni ad alta concentrazione di acido che noi non utilizziamo.
Si possono trattare anche le leghe fuse fino al 12%-14% di Silicio; le caratteristiche del rivestimento decadono con l’aumentare del tenore di silicio.
Su leghe adatte vengono eseguiti strati con spessori compresi tra 20 e 50 microns. La massima resistenza specifica all’usura si ottiene nel campo 40-50 microns.
Sulle leghe ad alto silicio gli spessori sono limitati a 10-20 micron.
L’aspetto dei pezzi trattati dipende dalla composizione della lega e, entro certi limiti, dai parametri di trattamento utilizzati; è in ogni caso molto variabile.
VARIAZIONI DIMENSIONALI
L’elevato spessore modifica sensibilmente le tolleranze di lavorazione. Occorre prevedere, dopo trattamento, un aumento dei diametri od un restringimento dei fori, e quindi modifiche dimensionali su tutte le parti in tolleranza, in funzione dello spessore dell’ossido. La formazione dell’ossido avviene a spese dell’alluminio sottostante e si accresce grosso modo per metà sotto la superficie originaria e per metà sopra.
Se il processo è accuratamente controllato è possibile prevedere più correttamente le variazioni dimensionali secondo il seguente criterio:
- per le leghe serie 6000, una volta lo spessore sul diametro. Esempio: 40 micron di spessore di strato aumentano il diametro di un albero di 40 micron.
- Per le leghe serie 7000, spessore x 0,8 sul diametro. Esempio: 40 micron di spessore di strato aumentano il diametro di un albero di 32 micron.
È necessario avere cariche della stessa lega e provenienti dallo stesso lotto di materiale, perché anche le sole variazioni di analisi di una stessa lega portano a spessori diversi.
Consultateci sempre in caso di dubbio; l’errore sulle tolleranze è il caso più frequente di anomalia che riscontriamo.
Noi garantiamo genericamente lo spessore dello strato; la garanzia sulle tolleranze deve essere preventivamente concordata. In molti casi, se concordato, possiamo anche effettuare un controllo strumentale delle tolleranze sulla linea di produzione.
Diverso è il caso in cui vengano effettuate satinature chimiche. In questo caso l’asportazione di materiale può essere rilevante, fino ad alcuni centesimi di millimetro sul diametro. L’asportazione può essere estremamente variabile. L’utilizzo della satinatura deve sempre essere valutato con attenzione, può richiedere la protezione di parti in tolleranza e deve comunque essere espressamente approvato.
POST TRATTAMENTI
I particolari ossidati duri possono essere forniti allo stato naturale oppure possono essere condizionati in modo diverso
E’ possibile effettuare:
- La colorazione nera
- La sigillatura del poro
- L’impregnazione con oli
- L’impregnazione autolubrificante a base di resina fluorocarbonica (PTFE)
Con alcune leghe è possibile sfruttarne le proprietà autocoloranti per ottenere, con diversi spessori, colorazioni tipiche come grigio perla, grigio, grigio scuro , grigio verde.
DUREZZE
Genericamente si ottengono microdurezze, misurate col penetratore di diamante, comprese tra i 400 e 500 Vickers, che possono essere entro certi limiti variate modificando i parametri del processo.
Si tratta di una durezza apparente dovuta al fatto che il penetratore frantuma il cristallo di ossido.
In pratica, tranne che per le leghe 7000 che sono un poco meno dure, sulle leghe serie 6000 gli strati devono resistere all’abrasione della carta abrasiva al corindone rosso grana 220, senza lasciare deposito evidente sulla carta. L’abrasivo della carta è ossido di alluminio, come lo strato di ossido anodico, ma elettrofuso.
Le durezze sono entro certi limiti paragonabili, però a svantaggio dello strato di ossido duro che si forma invece in soluzione acquosa e che contiene micropori, qualche molecola di solfato, ecc…
In ogni caso, uno strato di ossido di buona qualità, praticamente non viene abraso.
TENUTA A CORROSIONE
La tenuta alla corrosione minima soddisfa le prescrizioni della UNI EN ISO 7599. In funzione delle varianti di processo utilizzate e dei materiali trattati, può raggiungere valori molto elevati, in nebbia salina secondo UNI EN ISO 9227.
PARTICOLARI TRATTABILI
Trattiamo principalmente particolari meccanici in piccola e media serie , fino a centinaia o migliaia di pezzi, secondo la dimensione .
Corpi pompa, pulegge dentate, componenti per macchine da imballaggio, componenti per sistemi di manipolazione, componenti per macchine utensili, componenti di macchine tessili, componenti idraulici e pneumatici, componenti speciali per racing di auto , moto ecc..

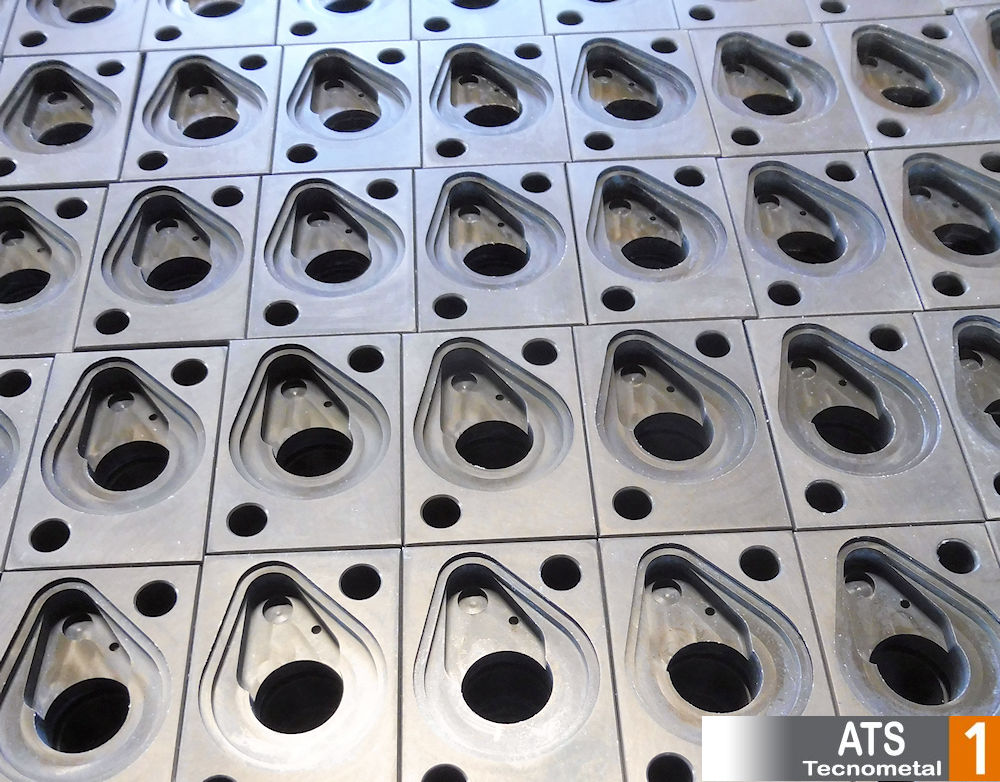
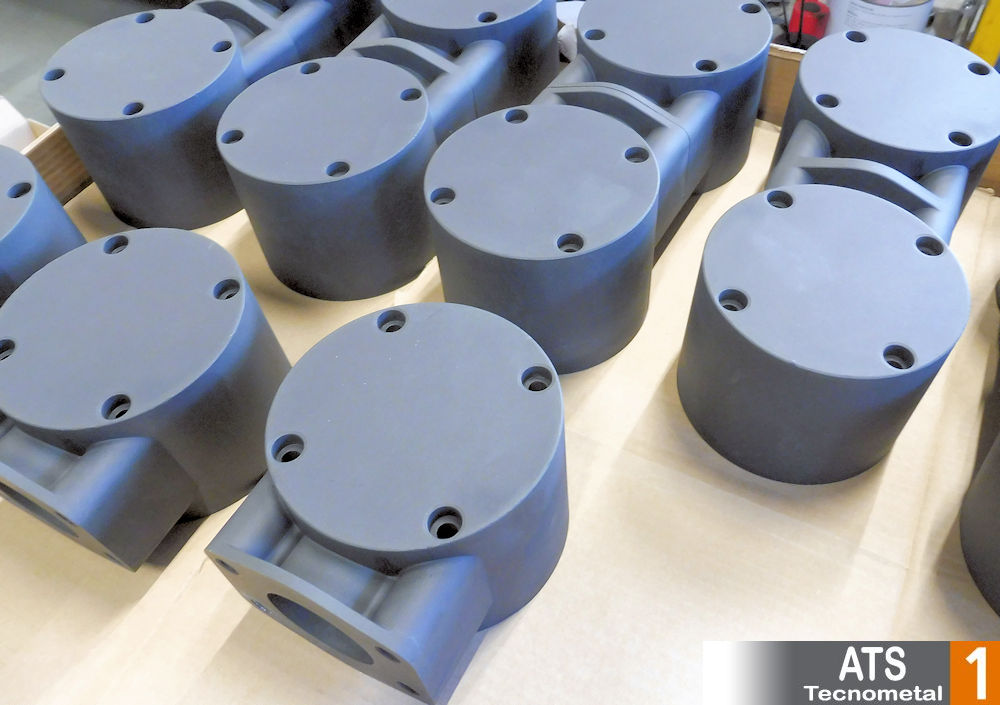
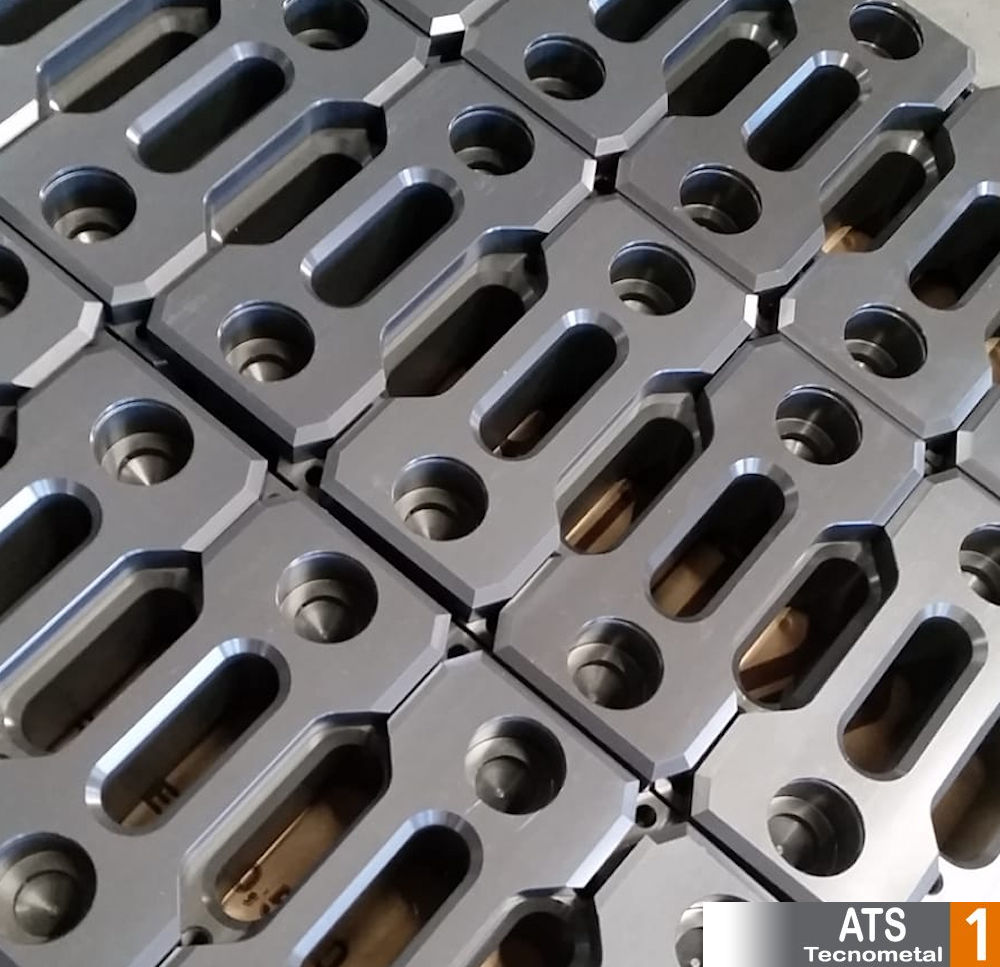
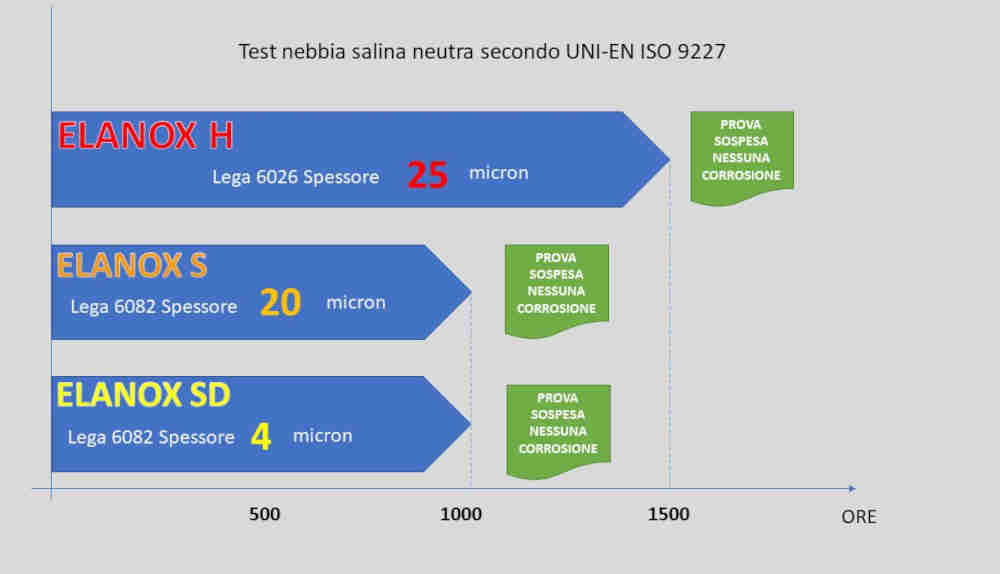